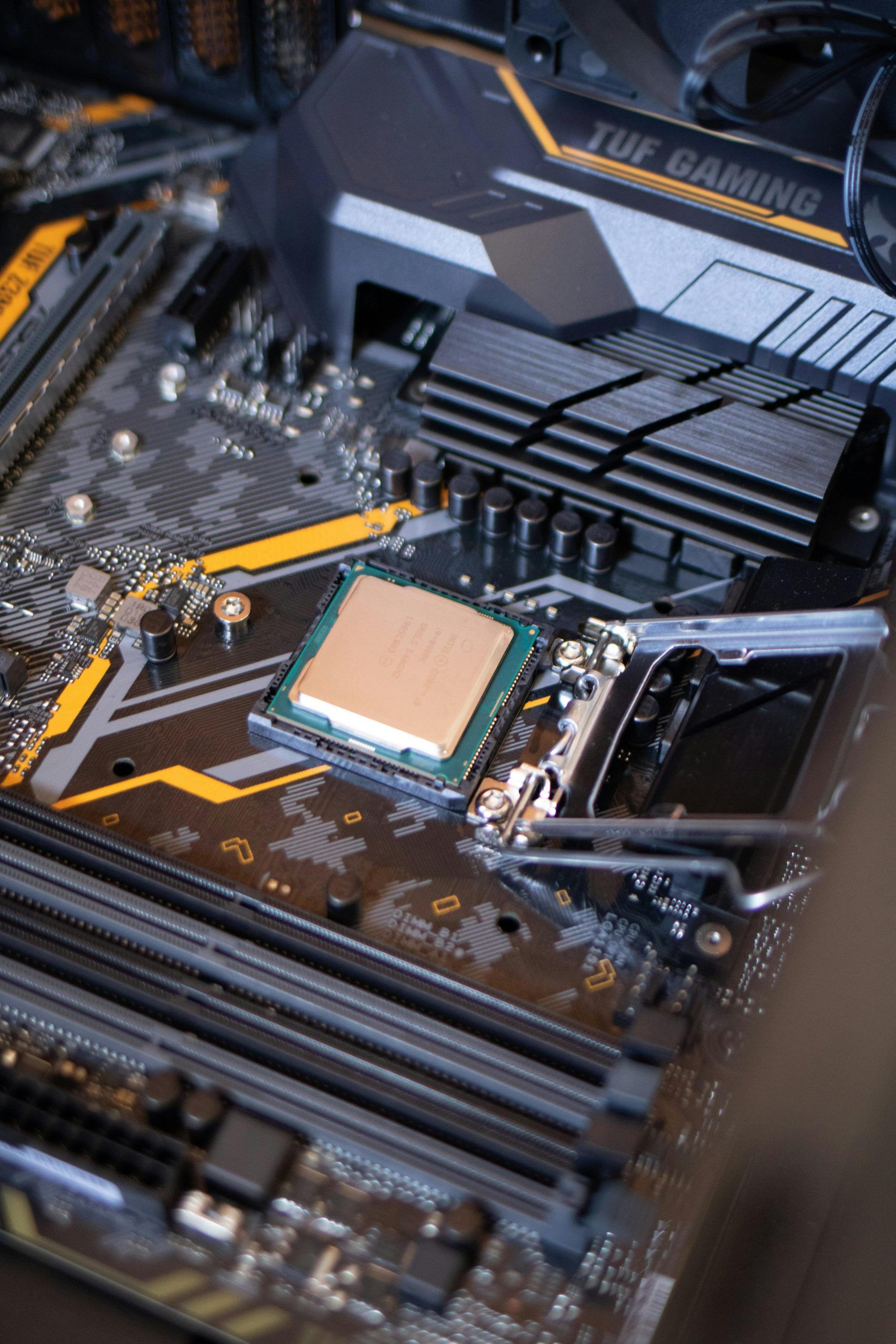
The electronic components validation is a fundamental procedure in the development and production of electronic devices. From sensors in cars to circuits in medical devices, the quality and reliability of electronic components have a direct impact on the safety and performance of many products that surround us every day.
If for companies, the electronic components validation is synonymous with reduction of failures, regulatory compliance and competitiveness on the market; for consumers, it is a guarantee of durability and operation even in extreme conditions.
In today's article we will see what the validation of electronic components is, how it is done and the international standards that regulate it.
What is the Electronic Components Validation
By electronic components we mean all those small elements - such as resistors, capacitors, integrated circuits and sensors - that constitute the heart of electronic devices.
Validating an electronic component means subjecting it to a series of tests to verify its resistance, reliability and stability, in particular when it is subjected to critical environmental conditions.
Tests can concern different aspects: mechanical, electrical, duration. In this context we will focus on environmental tests, that is, those that evaluate the behavior of components in extreme temperature and/or humidity conditions.
Perform
Extreme Testing
Discover the new series of Environmental Chambers for controlled climate testing
How Electronic Component Validation Works
In the context of environmental tests, the electronic components validation is carried out with the use of environmental chambers.
Environmental chambers are part of the larger family of climatic chambers and are the type intended for so-called "extreme" tests, that is, tests that touch very high or very low values
Among the most common tests performed inside an environmental chamber are:
- Burn-in test: often performed on electronic boards, the Burn-in test is used to unmask design defects by short-circuiting the component. We talked about it in more detail here.
- Cyclic temperature test: the component is subjected to repeated hot/cold cycles, for example going from -40°C to +125°C, with pauses of a few hours at each end. This type of test highlights problems due to thermal expansion, defective soldering or incompatible materials.
These tests help predict how the component will behave in reality, reducing the risk of malfunctions once installed in the final product.
Standards for the Electronic Components Validation
The validation of electronic components must follow precise guidelines, established by internationally recognized bodies.
These standards define the methods, times and acceptance criteria of the tests, allowing manufacturers to demonstrate the conformity of their components.
Here are some of the most globally recognized standards:
- IEC 60068-2 – Environmental testing for electronic components
- MIL-STD-883 – Qualification of microelectronics for military and aerospace applications
- IPC-TM-650 – Reliability of printed circuit boards in extreme thermal conditions
You cannot find the ideal chamber for your test?
Create your own environment, according to any test requirement
The FDM Environmental Chamber for the Electronic Components Validation
For over 70 years, FDM Environment Makers has been a leader in environmental simulation, providing the public and private sectors with the tools necessary for research, development and production.
Our environmental chambers are the ideal tools for carrying out the tests required for the validation of electronic components.
Thanks to the most advanced technologies in the sector, our chambers are able to perform all the tests prescribed by international standards.
Furthermore, our technicians are always available to listen to the specific needs of each customer to design the customized chamber that meets their needs.
Download the White Paper below to learn more.
Would you like to receive a quote or do you have questions about the product?
Contact us to receive more information about this Product.