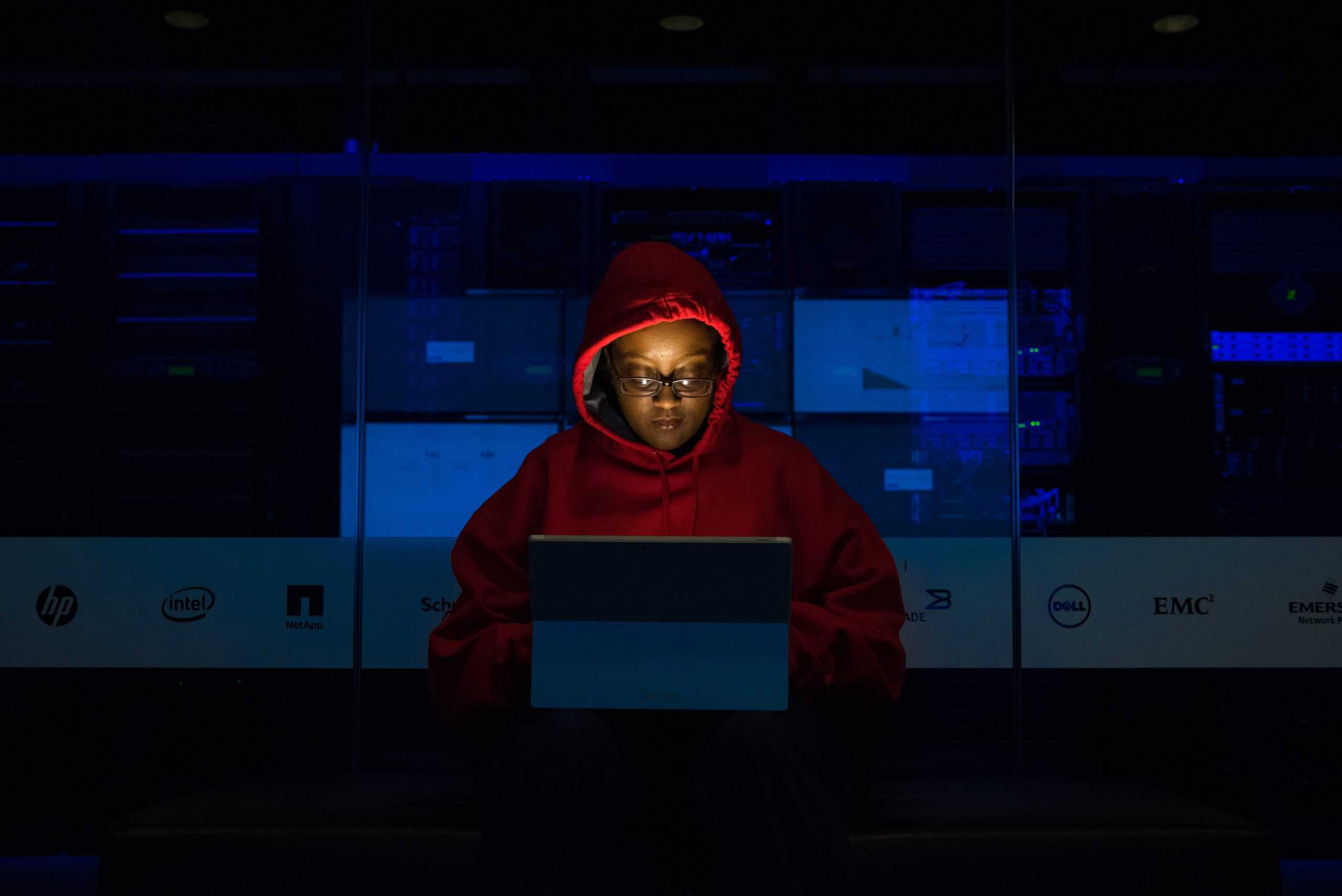
As the demand for electronic components, especially semiconductors, continues to grow rapidly, one of the challenges that industry faces, is working on the time taken to test those components.
Traditionally, Temperature Humidity-Bias testing (THB) has been the solution. It is a very valid one, but taking 1000 hours to be completed, it represents today a significant delay for modern industrial processes.
Precisely for this reason another type of test was devised: the HAST test, Highly Accelerated Temperature and Humess Stress Test.
Che cos’è l’Hast Test
Taking between 96 and 100 hours per test, and in some cases even less, the HAST test provides significant time saving, that can have a great impact on any business.
For this reason, the test has quickly become the most dominant of the endurance test methods for semiconductor devices. While primarily connected with semiconductor testing, HAST testing is used on a variety of both hermetically sealed and unsealed compact electronic components, to provide fast testing results for several situations and requirements.
Perform
Climate Stress
Discover the new series of Climate Chambers for controlled climate testing
HAST testing standards
Allthough, time is not the only difference between the two tests: for example, the THB testing holds a 85°C/85% R.h. condition, as the samples are subjected to Bias loads. However this has become less relevant today, due to the new technology used for packaging and passivation materials.
By contrast, HAST test conditions use a high temperature of at least 100°C and usually around 105°C, along with high relative humidity of around 85%, in combination with a high atmospheric pressure of up to 4 atmospheres. There is also a saturated version of the HAST test that uses a 121°C temperature and relative humidity of 100%. If components are tested with power on, in most cases the test is performed with 85%RH. These environmental parameters provide an accelerated method of component reliability testing, that quickly finds faults and defects that could emerge during long-term use.
There are several standards for HAST tests from the IEC, JESD, JIS and JEITA, all indicating different combinations of temperature and RH, and are used for different situations. The most common are:
- IEC 60068-2-66 - Used for hermetically sealed compact electronic components.
- IEC 60749-4 - Used mainly for semiconductors.
- JESD020C – Reflow soldering
- JESD22-A104D – Temperature Cycling testing to cover component and solder interconnection testing
- J-STD-002D – Test per resistenza all’umidità accelerata, autoclave non distorto
- JESD22-A108B – High Temperature Operating Life (HTOL) test
- USED JESD22-A102C. – Used for accelerated humidity resistance testing of non-hermetically sealed semiconductor-based devices
- USED JESD22-A110C. – Used for non-hermetically sealed semiconductor-based devices, while powered, to evaluate reliability
- JESD22-A118 – Evaluates the reliability of unpowered non-hermetically sealed semiconductor-based devices
- JIS C60068-2-66 – For testing compact electronic components
- JEITA ED-4701/100 103 Method– Tests the durability of semiconductors that are stored or used within high temperature and humidity-based atmospheres
Perform
Extreme Testing
Discover the new series of Environmental Chambers for controlled climate testing
How to Perform HAST Test with a Climatic Chamber
The highly accelerated stress test, also known as HAST, is performed with specific testing chambers, developed to meet all requirements from the test.
As mentioned above, these chambers are meant to replace existing THB test chambers, which use wet/dry bulb mechanisms to control humidity.
The HAST chamber, that manages temperature and humidity, is key to delivering faster results in all conditions.
HAST testing is particularly useful during product changes where adjustments could potentially accelerate metal corrosion, with results being obtainable way faster than with other solutions, having then significant impact on development times. The HAST test is the best option for testing any kind of moisture driven corrosion .
It also provides complete test results of all components subject to deterioration, of overall performance, including performance of sealed plastic components in a variety of conditions, including a vibration test . The HAST approach provides the real impact test, which offers an overview of product performances .
Conclusion
With its flexibility providing a variety of test results in a short time, HAST testing is essential for the modern industrial production cycle. The HAST testing process allows both saturated and unsaturated testing of components within the test cycle, for plastic sealed components or for others designed to be environmentally sealed.
Whatever testing standards are used, the ability to have tests completed in days, rather than months, creates new opportunities for product development. By fastening testing processes, companies are able to deliver faster responses to always changing production requirements, thus improving performances and user satisfaction.
Would you like to receive a quote or do you have questions about the product?
Contact us to receive more information about this Product.